DSG Notum Pro
薄木框锯机
优势总结:
Notum - 卓越体验
- 薄木框锯机发明者匠心打造
- 精准与性能,满足一切需求
- 全球应用,彰显专业与智慧
久经验证,创新不止
- 电子控制的精密进给
- 提高中心锯框应力
- 切割高度 266 mm
- 完美的锯框系统
- 经过优化的吹风系统
简便的操作
- 以人体工学为本,确保每个部件都能轻易的被接触到
- 可调节的电动控制压轮升降装置
- 触摸屏操作起来十分简便
- 中央控制台
Notum - 卓越体验
薄木框锯机发明者匠心打造
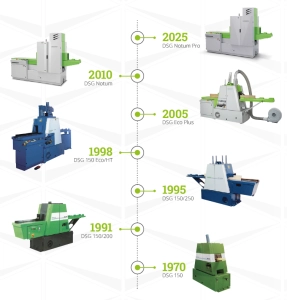
DSG Notum Pro 沿袭了 WINTERSTEIGER 的传统,将最佳品质与资源的最佳利用结合在一起。这一传统始于 1970 年推出的前代机型 DSG 150,如今已遍布全球各大洲。凭借全球技术领导者的丰富经验,WINTERSTEIGER 现推出新一代框锯机 DSG Notum Pro。借由高精确度、极小的锯路以及可直接涂胶的表面,WINTERSTEIGER 一直以来都在薄木框锯机领域占有龙头地位。从研发到生产,从设备、工具到服务的完整性,确保了 WINTERSTEIGER 的机器性能稳定、持久。
用最好的技术、最优的价格并以最经济的形式实现顶级品质!
全球应用,彰显专业与智慧
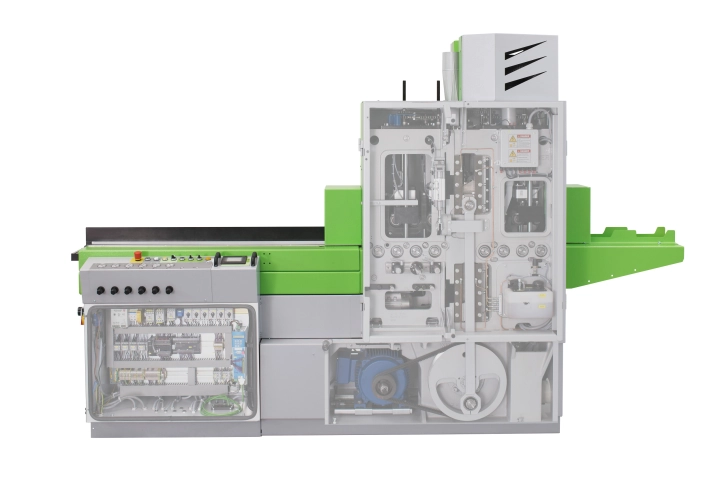
全球应用,彰显专业与智慧
目前世界范围内有超过 2000 台 WINTERSTEIGER 的薄木框锯机正在使用中。每一台正在工作的机器都代表着专业与智慧。DSG Notum Pro 正是这一成功传奇的延续,WINTERSTEIGER 与客户共同书写新的篇章。
如何能超出客户的预期?
一系列的产品优势是实现这个目标的基础
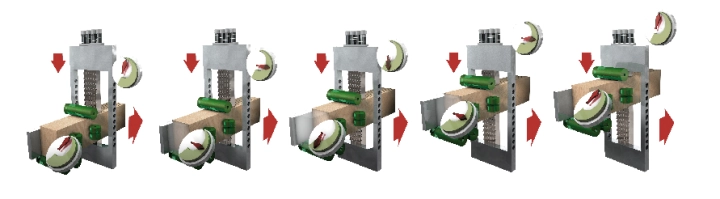
在进行任何投资之前,都必须经过事先的认真考虑。确定是否满足节约的标准。DSG Notum 的基本型号已做到这点,它提供多种难以置信的功能,确保更高的精度,更高的产量和更人性化的设计。它可以为您保证实现高满意度和稳定的性能。
电子控制的精密进给。
在进料和出料区有一个电子控制的精确进料系统操控送料轮。令每一粒锯齿在每一点位置可准确切除一定数量的木材。并且是在锯框移动的每一个时间点里都可以计算出精确的去除量。这种技术使锯片寿命更长,木片表面光滑,精度高。
产品特性概览
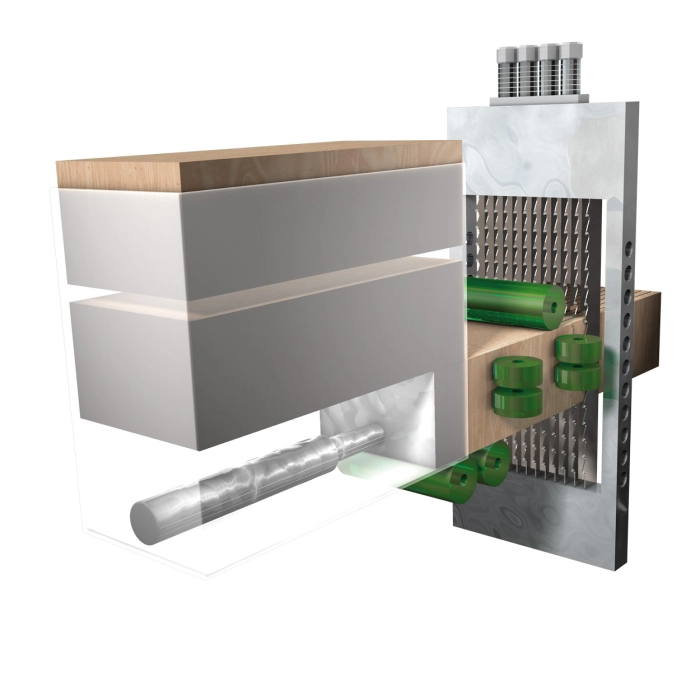
锯条库
锯条库可以保证不间断地输送木块。使一个人可以同时操作几台机器。
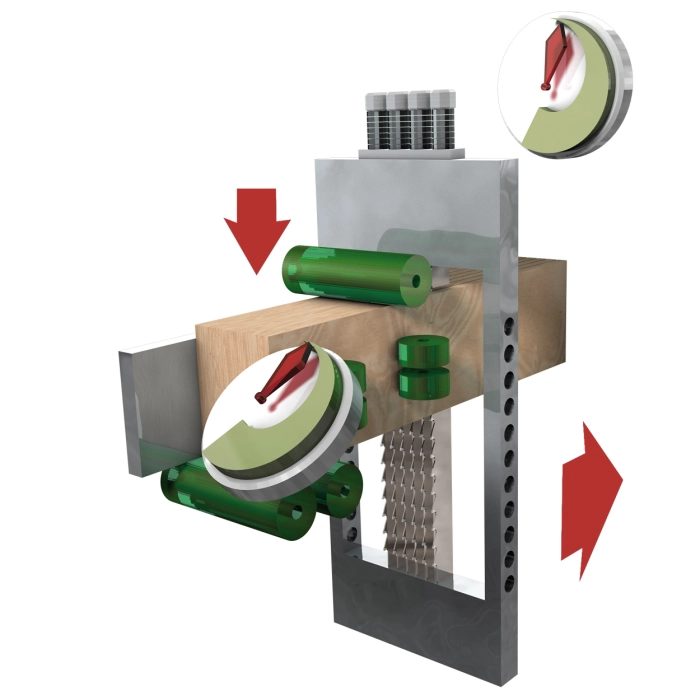
电子控制的精密进给
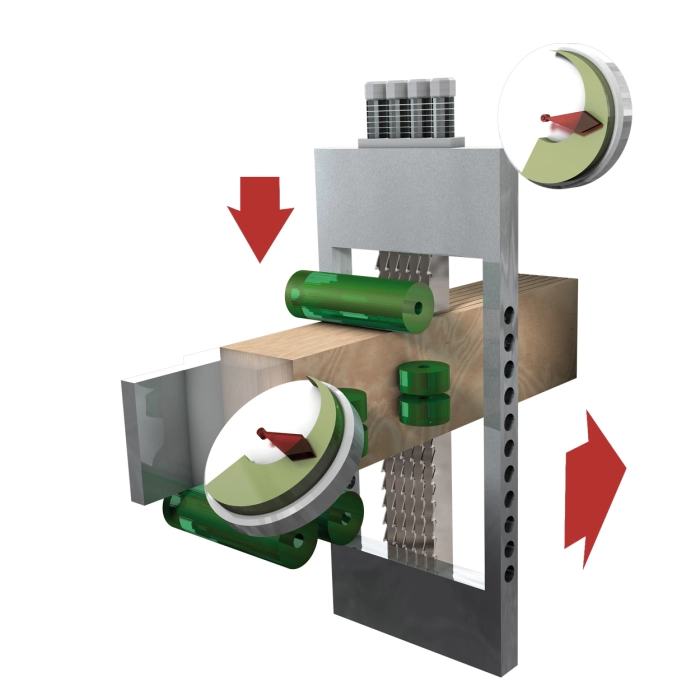
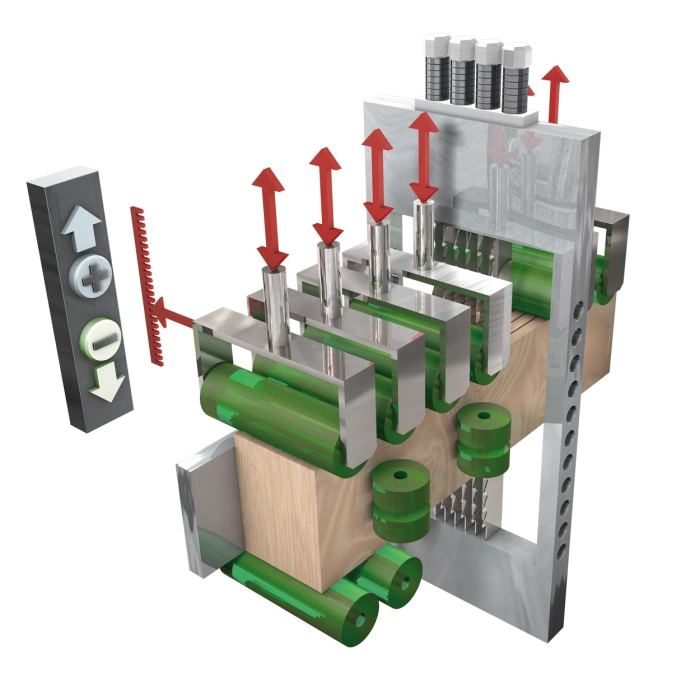
压轮升降系统
电动压轮升降系统可自动调节木块高度并最大限度地缩短设置时间。
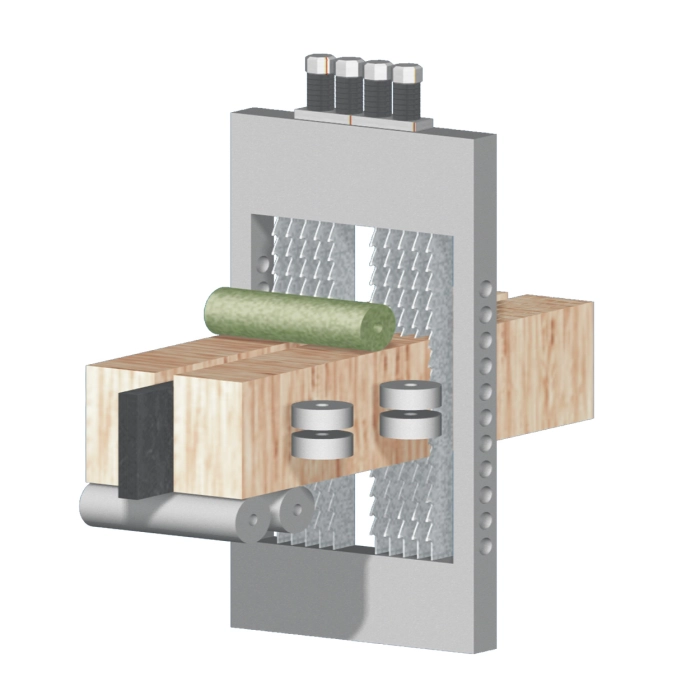
中靠挡
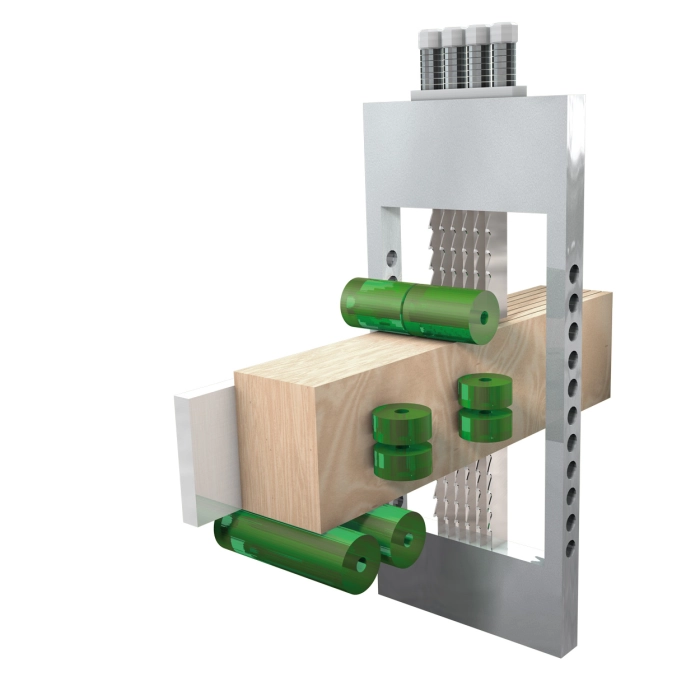
侧面挡块
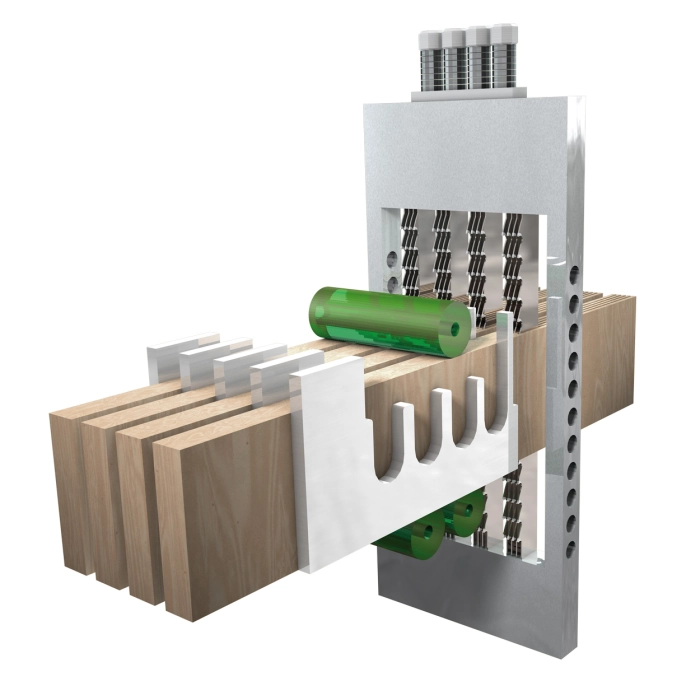
多排式送料系统
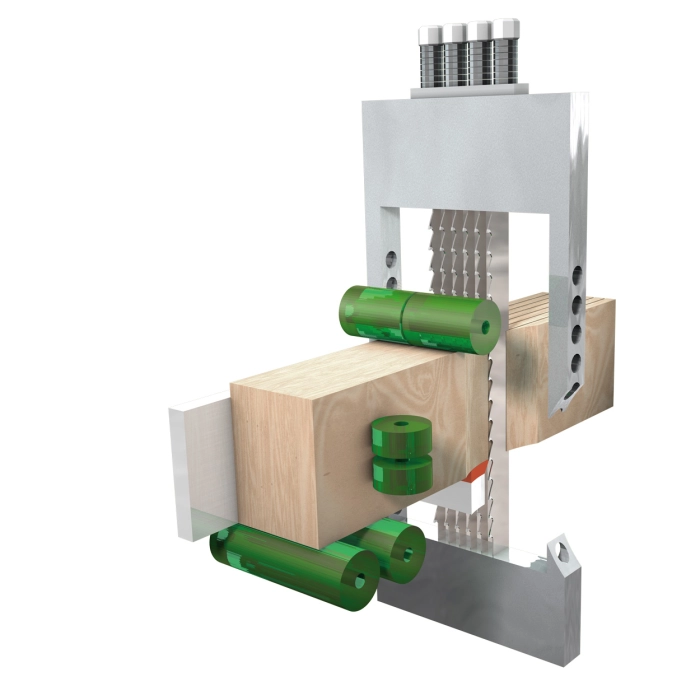
防撕裂装置
标准已配备的防撕裂装置保证木块底部在锯条离开时不被撕裂。
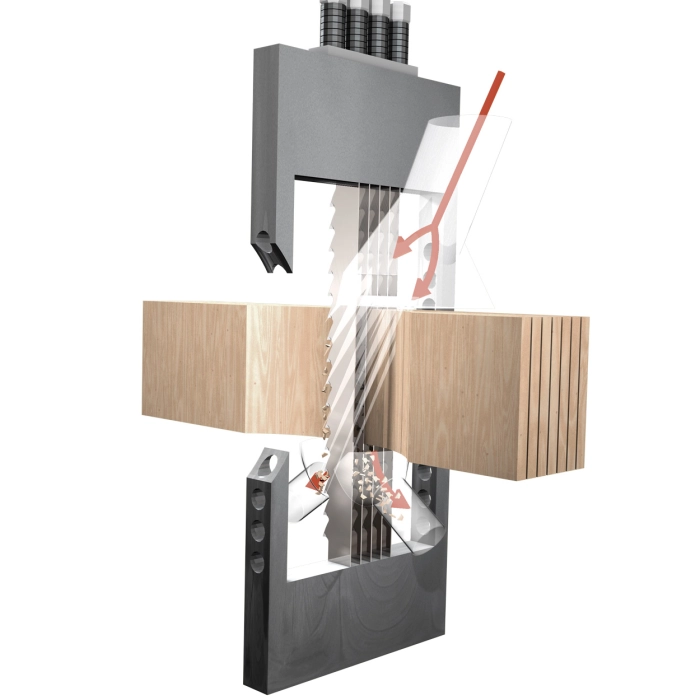
吹风装置
锯切区的上方有空气直接喷出,在锯齿外围形成持续的气流,当锯切时,吹走木屑。由于减少了摩擦,有助减慢锯齿钝化,同时也不会使锯条温度升高。用户优势:保持锯条较长的运行时间,木块进给无木屑困扰,能更有效加工一些难处理的木材。
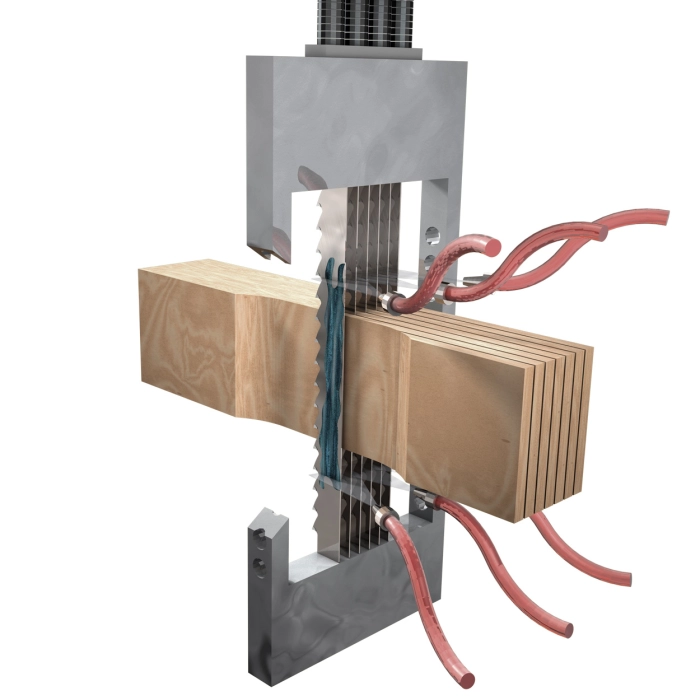
喷雾系统
该系统可喷出防黏液,能够防止锯片粘上木屑树脂。喷射频率可以根据木材种类和需求进行调节。
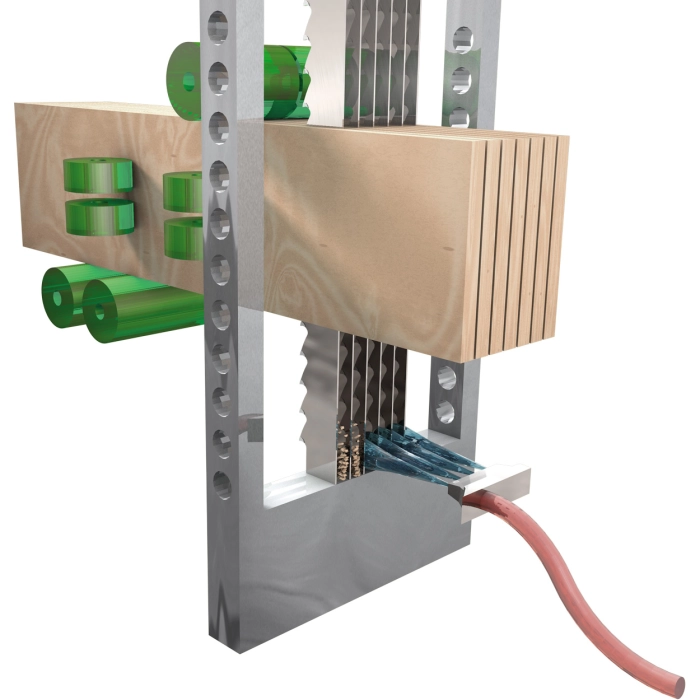
锯湿木系统
除了吹风装置和喷雾系统外,还可以用压缩空气吹走锯湿木后残留在锯框底部的沉重木屑。
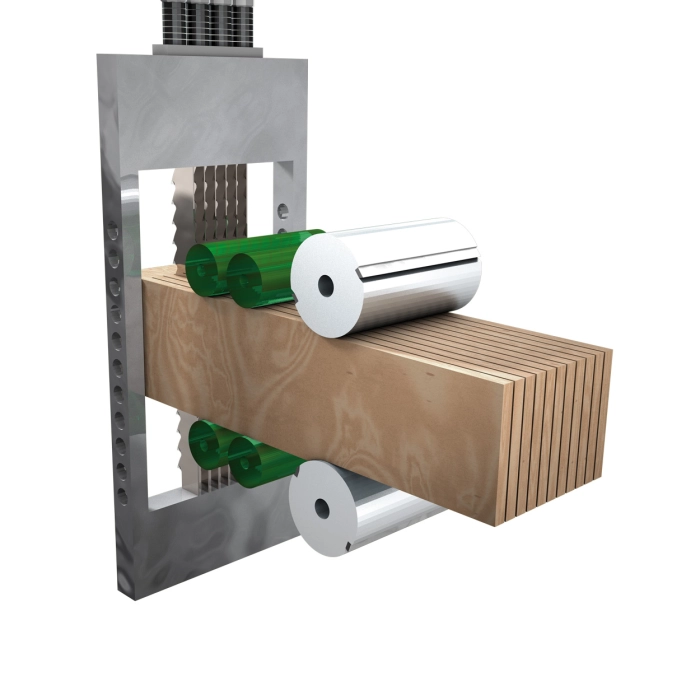
顶底刨装置
新开发的顶底刨以单边轴承承托,非常方便接触到机器组件,结构紧密,更换刀具简单。
用户优势:木片边角非常精确,可以直接胶合,在木片顶侧没有送料轮的压痕,而且木片平行度极好。
提高中心锯框应力
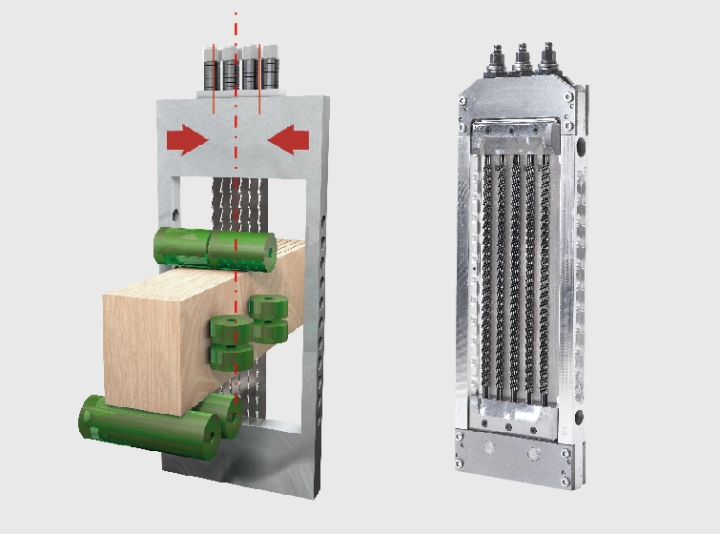
提高中心锯框应力
对称的锯框结构保证了锯片应力均匀。从而改善了锯切精度,提高了锯片的使用寿命。每一个锯片都可以快速、简便的更换。
亮点
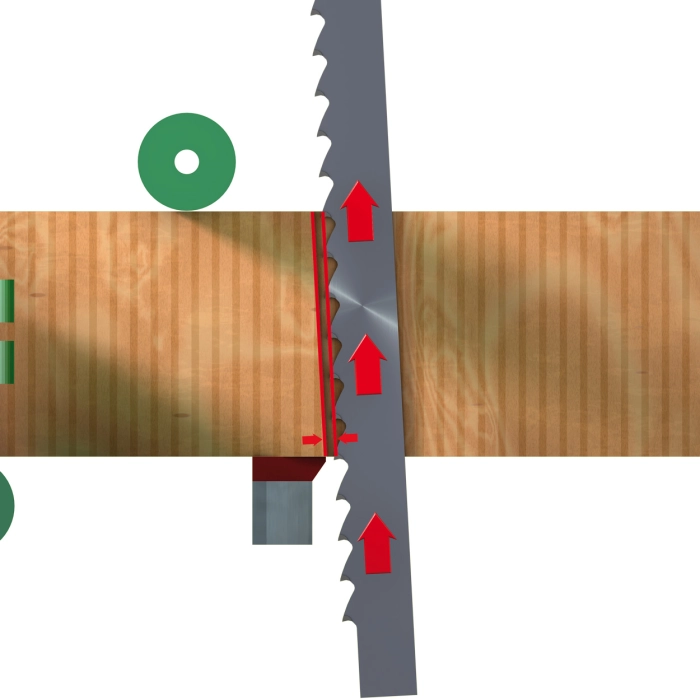
稳定的空走
木块传送和锯框上下摆动,两者之间的完美协调,一方面控制锯框摆动幅度,另一方面确保锯框向上移动时是空走,往下时才进行锯切。和 WINTERSTEIGER 的吹风装置一起,保证实现最佳切割性能。
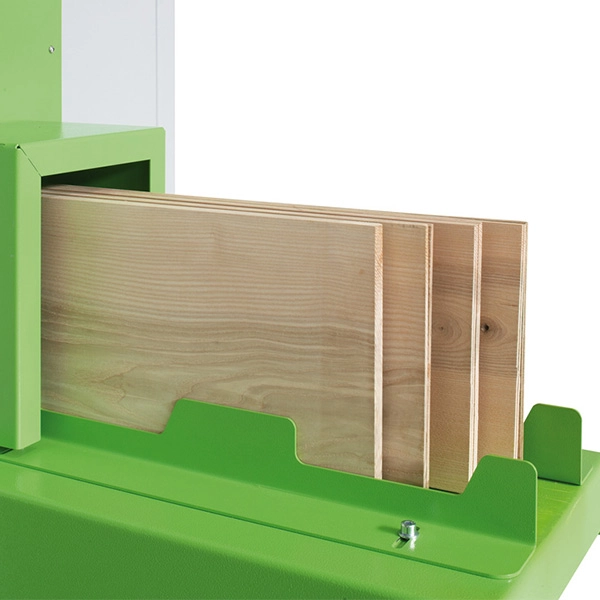
切割高度 266 mm
WINTERSTEIGER 通过将切割高度标准化为 266 mm,再次彰显了其以客户需求为导向的一贯理念。这样可以在初级加工的时候就将用来生产超宽的木地板面板、门框和护墙板的薄木板以 WINTERSTEIGER 著名的精确度和最小 1.1 mm 的锯路切割出来。
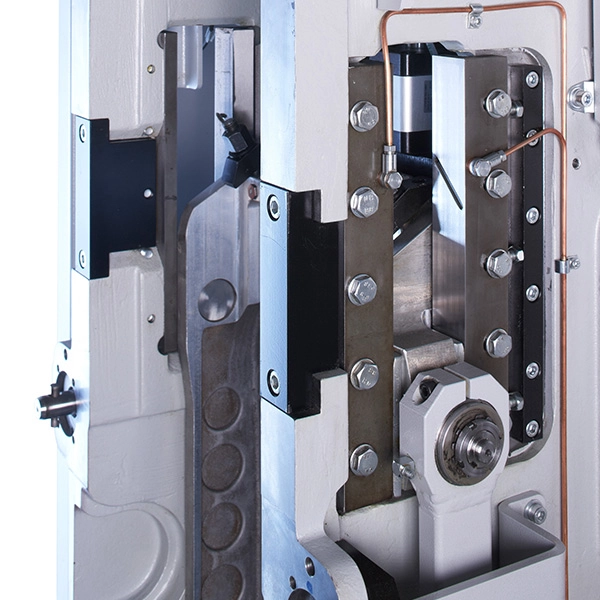
完美的锯框系统
为了进一步优化多年来口碑良好的、移动自由平滑的薄木锯准则,我们对原有的锯框运动的核心元素进行了改进。我们在锯框结构上做了改进和加强,结合易维修的结构设计,使得机器在克服新切割高度挑战的同时,也能够更高效的运作。
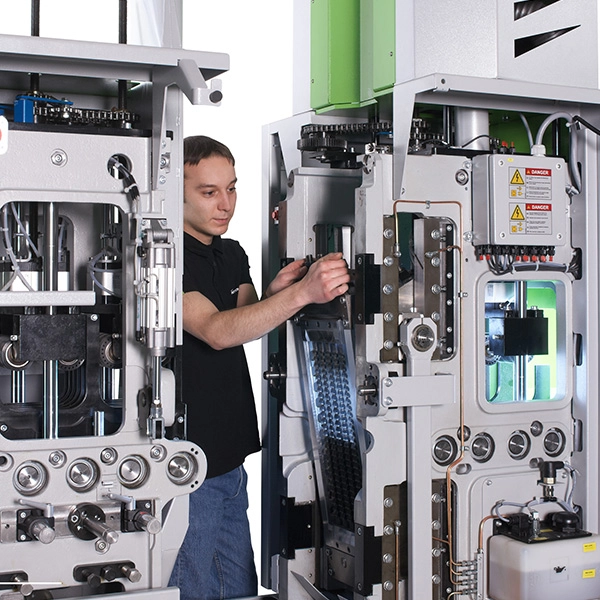
使用极其方便
革命性的设计使操作员可以容易地接触到机器的所有组件。这样就可以在机器打开的时候简便的进行锯框更换。调试、锯条更换和维修时间都大大缩短,延长了机器的可使用时间。
无间隙直线导轨确保精确移动。强有力的闭锁装置可以保证机器运作时的稳定。
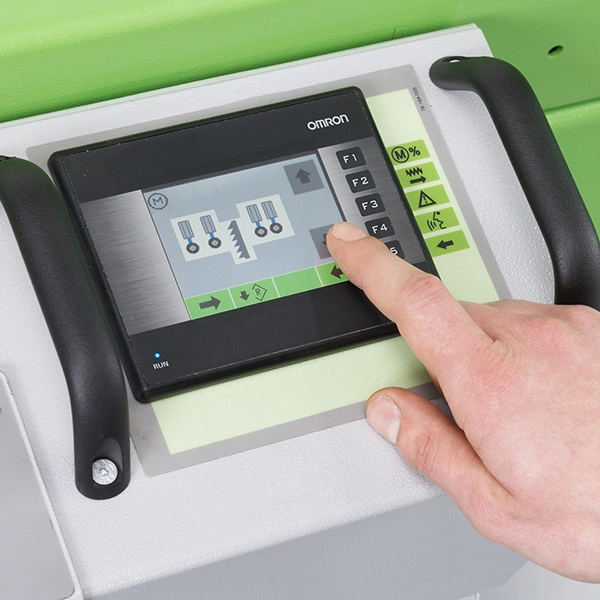
操作简单
紧凑和一目了然的控制面板,可轻而易举地修改参数,调整菜单,还配有维护操作说明。
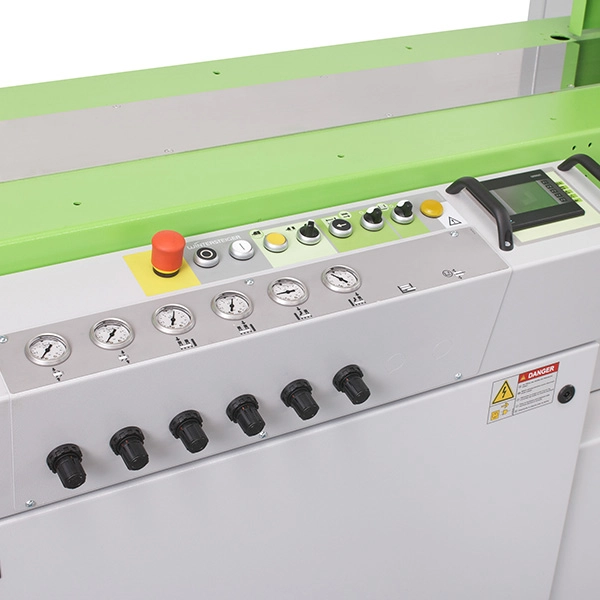
中央控制台
所有的控制参数都可以在中央控制触摸屏、操作开关和压力调节器上设置。这代表着从现在开始不再需要机械设置工作了。操作台具有自动防振功能。因此所有的气动式和电动组件都会避免受到振动的影响。最直接的优势就体现在机器使用寿命更长以及控制元件的可支配性更高这两方面。
各种木材导向系统
严苛的要求需要个性化的解决方案。
WINTERSTEIGER 为此提供个性化定制的木材导向系统:
侧靠档和中靠档
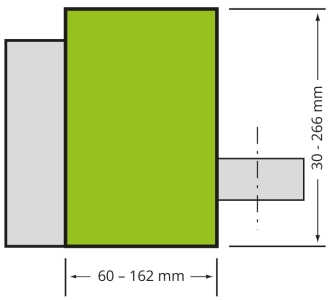
在侧面挡块位置,木块通过气动控制的压轮,沿着侧靠档的基准面移动。
木块宽度:0 ~ 162 mm
木块高度:30 ~ 266 mm
中靠挡
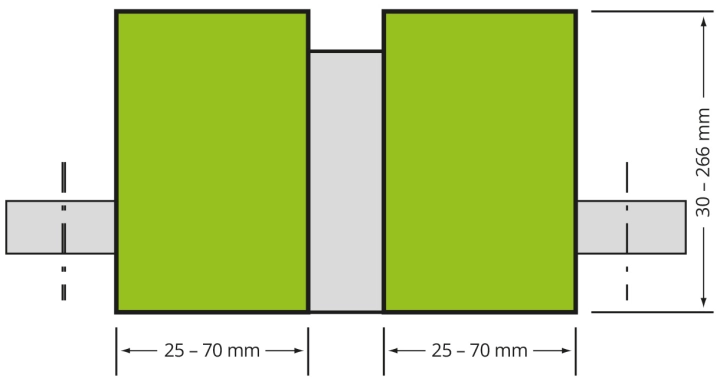
在中靠档位置,两个木块通过气动控制的压轮,同时沿着中靠档的左右两侧基准面移动。
木块宽度:2 x 25 ~ 70 mm
木块高度:30 ~ 266 mm
多排式送料系统
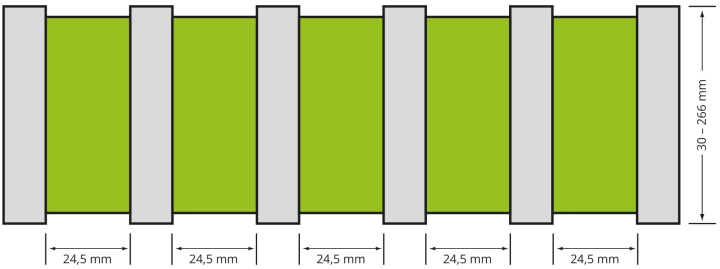
该系统补料简单易操作,可以同时加工多个木块。
通道设计:根据客户要求
通道数量:2 至 5 个通道
木块高度:30 ~ 266 mm
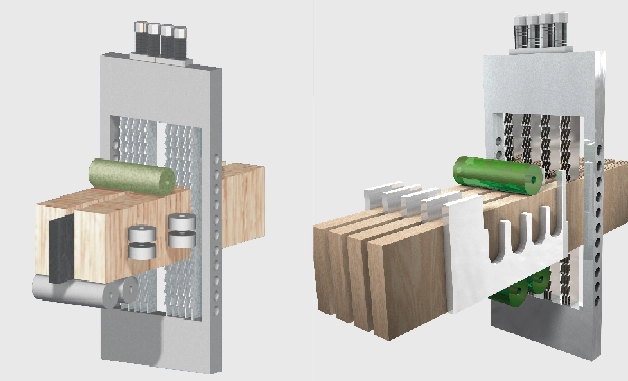
由于木块进口位以锥形设计,因此木块不会被卡住(预先刨过的木块可以去除应力!)
特别制作的导轨能够使木块准确地进入到锯口中
自主开发生产的锯片。
要求严苛的客户需要定制型刀具。
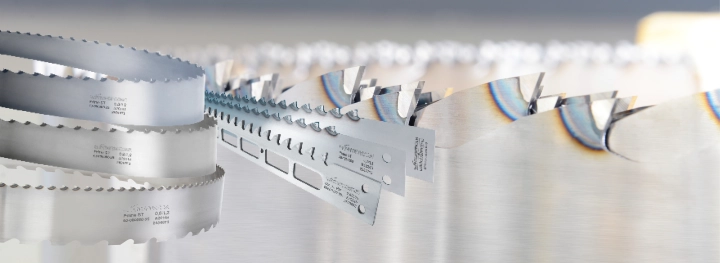
WINTERSTEIGER 根据客户要求提供优质材料、合适的锯条尺寸和锯齿几何形状。
WINTERSTEIGER 的薄切割框锯和带锯令人折服!
- 最优解决方案
- 经济效益极高
- 可信赖的合作伙伴:
WINTERSTEIGER 售后服务。
交货的完成即意味着服务的开始。
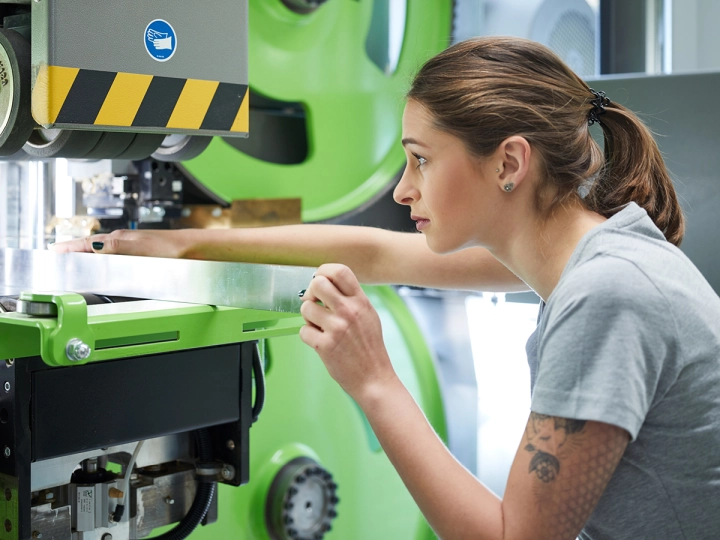
WINTERSTEIGER 售后服务。
交货的完成即意味着服务的开始。
您的 WINTERSTEIGER 客户顾问将很乐意为您提供量身定制的解决方案!